Research
Summary
The Materials Science Laboratory is engaged in material development research with the keywords "mechanochemical" and "interface".
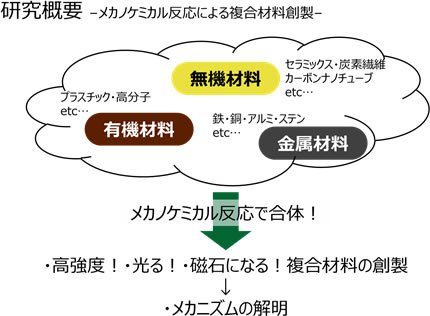
Specifically, we are developing new composite materials by applying mechanical external force to metallic materials such as iron and aluminum, inorganic materials such as ceramics and carbon fiber, and organic materials such as plastics and resins.
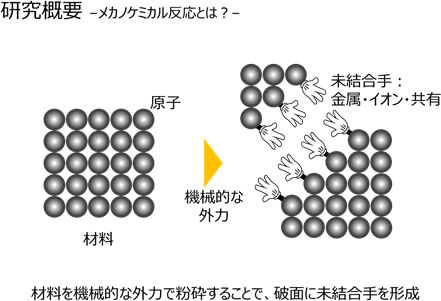
What is a mechanochemical reaction? All materials are atomic aggregates. Atoms are connected by various forces. When an external force exceeding this force is applied to the material, the material breaks, but on the fracture surface, as shown in the figure, there is a dangling bond. This is the hand used to bond with the next atom before destruction. If a different element is brought close to this bond, a new material will be created. This is the basic mechanochemical reaction principle.
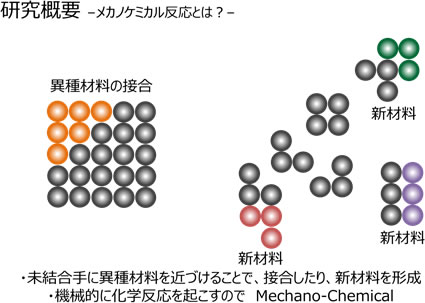
The material formed by the mechanochemical reaction has a boundary between the original material and the newly combined material. This is the "interface". Various interesting phenomena occur at this interface, which are the factors that give rise to new functions in the material as a whole.
Development of Novel soft magnetic material
What percentage of the total annual power consumption in Japan is the amount of electric power used to drive motors? What a 51%. As of 2003, Japan's domestic electricity consumption was 985 billion kWh, half of which is used to drive motors. Isn't it a bit different from the image? That's because motors don't just achieve visible movement. For example, air conditioners. At first glance, it doesn't seem to use a motor, but it uses a motor to drive the compressor.
The motor converts electric energy into kinetic energy. How much power is consumed by the conversion loss? That is 3.4% of Japan's total annual power consumption. This is equivalent to 7 thermal power plants. Therefore, it is very important to reduce the conversion loss of motor power/kinetic energy.
Motor loss can be divided into iron loss, copper loss, and mechanical loss. We are researching materials that can reduce iron loss.
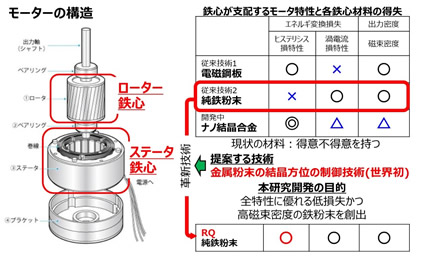
As shown in above, the motor has a component called an iron core, which plays an important role in converting electrical energy into kinetic energy. However, the iron loss described above is also generated in the iron core. Iron loss can be further classified into hysteresis loss and eddy current loss. Magnetic steel sheet is a widely used material for iron cores. This material has excellent hysteresis loss characteristics. A new iron core material that has been studied since the 90s is pure iron powder. An iron core can also be made by compression molding pure iron powder. The dust core can suppress eddy current loss. In other words, electromagnetic steel sheets and pure iron powder each have advantages and disadvantages.
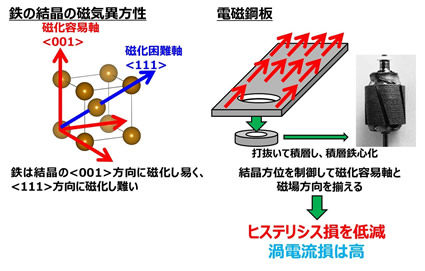
Why is the hysteresis loss of electrical steel sheets so low? That is because it makes good use of the properties of iron. The dice on the left of the figure are iron unit cells. When these unit cells gather, crystal grains are formed, and the aggregate of these crystal grains is the iron that you usually see. Iron has the property of being easily magnetized in the direction of the red arrow of this unit cell and difficult to be magnetized in the blue direction. This red direction is called the easy magnetization axis. To explain what it means to be easily magnetized, from an application point of view, it means that the current flowing through the motor can be efficiently converted into magnetic flux. This means that a small amount of current will generate motor torque. In addition, since the current can be efficiently converted to magnetic flux, the above-mentioned hysteresis loss is also reduced. In other words, you can make a powerful but small motor. It is the electrical steel sheet that artificially controls this easy-to-magnetize axis, and the laminated steel core is made by stacking the electrical steel sheets. It is called a laminated iron core because it is made by stacking steel sheets.
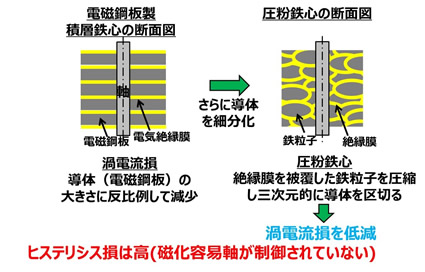
Next, why is the eddy current loss of pure iron powder low? Let's take a look at the cross section of the laminated iron core on the left. The laminated iron core is not just a stack of iron cores, but an insulating film is sandwiched between them. The reason is to suppress the eddy current generated when a current is passed through the motor. The loss due to eddy current is expressed by the following equation.
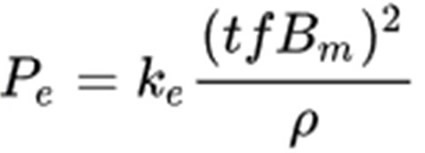
With this formula, t is the plate thickness. Therefore, if the plate thickness is reduced, the eddy current loss is reduced, so in order to reduce the plate thickness per sheet, an insulating film is sandwiched between them. However, due to its structure, the laminated iron core can only sandwich the insulating film two-dimensionally. Therefore, the powdered iron core was conceived, and the iron core is made after coating the iron particles with an insulating film as shown in the figure on the right. Therefore, iron, which is a conductor, can be separated by an insulating film, and eddy current loss can be further reduced. However, unlike electromagnetic steel sheets, pure iron powder does not have an easy-to-magnetize axis.
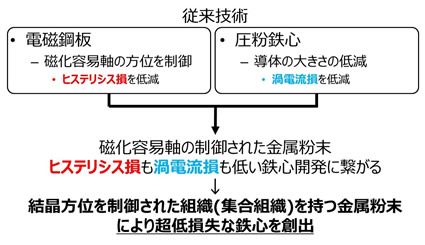
We believe that if we can control the easy axis of magnetization in iron powder, we can make an iron core with low hysteresis loss and low eddy current loss. If you would like to know more, please download the paper from the link below.
https://aip.scitation.org/doi/abs/10.1063/1.4930915
https://www.sciencedirect.com/science/article/pii/S0032591017306538
https://drive.google.com/open?id=1YhtKw7vBiwS-dwIYB7vuYBajaMc4MB0B
Related papers
Satoshi Motozuka, Tomoya Ikeda, Tomoya Miyagawa, Hisashi Sato, Masahiko Morinaga, “Formation process of the {001} fiber texture on iron particles using simple ball milling”, Powder technology 321, 9−12, (2017). IF2016=2.942
Satoshi Motozuka, Motohiro Tagaya, Kotaro Hayashi, Masahiko Morinaga, “Texture Formation in Iron Particles Using Mechanochemical Milling with Graphite as a Milling Aid.” AIP advances, 5, 097127 (2015). IF2014=1.590
Development of Novel material using molecular orbital calculation
We are developing materials using a computer simulation called the molecular orbital calculation method. A material is an assembly of atoms, which are composed of nuclei and electrons. The molecular orbital calculation method can analyze how electrons exist around the nucleus. Atoms and atoms form molecules and crystals by assembling them, and electrons play the role of "glue" that attaches the atoms to each other. Therefore, the strength and properties of the material can be predicted from the behavior of electrons.
The figure below is an example of molecular orbital calculation for hydrogen atoms and hydrogen molecules. The brown sphere in the center on the left of the figure is the nucleus of hydrogen, and the light blue and yellow parts show the distribution of electrons. In other words, if you perform a molecular orbital calculation on a single hydrogen atom, you can see that there are electrons on the left and right of the hydrogen atom. Next, if you perform a molecular orbital calculation by arranging two hydrogen atoms side by side as shown on the right of the figure, you can see that electrons exist between the nuclei of the hydrogen atoms. Since the nucleus is composed of positively charged protons, the negatively charged electrons act as "glue" and stick them together to form a hydrogen molecule.
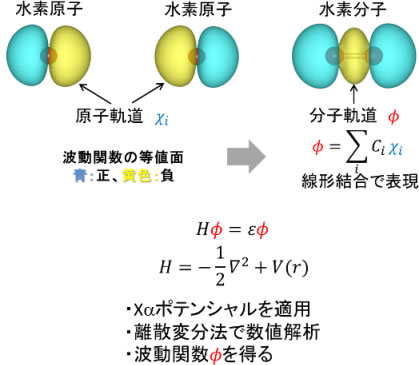
We believe that if we can control the easy axis of magnetization in iron powder, we can make an iron core with low hysteresis loss and low eddy current loss. If you would like to know more, please download the paper from the link below.
We use this molecular orbital calculation method to predict the shape of precipitates in metallic materials and develop materials that show fluorescence. The figure shows the behavior of electrons when a molecule called hydroxyquinoline and ceramics called hydroxyapatite are brought close to each other. Hydroxyapatite is approaching hydroxyapatite little by little from the left of the figure. You can see that as they get closer, the electrons of each other influence each other.
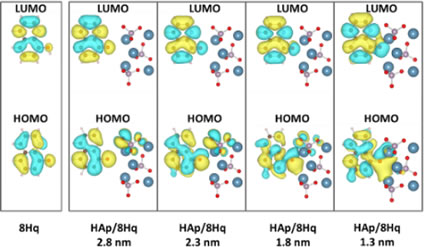
As a result of the interaction of electrons, the hydroxyquinoline and hydroxyapatite complexes synthesized by the mechanochemical reaction actually exhibit different fluorescence than when they exist alone.
Motohiro Tagaya, Satoshi Motozuka, Toshiyuki Ikoma, Junzo Tanaka, “Mechanochemical Preparation of 8−Hydroxyquinoline/Hydroxyapatite Hybrid Nanocrystals and Their Photofunctional Interface.” Insdustrial & Engineering Chemistry Research, 51, 11294−11300 (2012).